Reliable thickness measurement values even at maximum production speeds
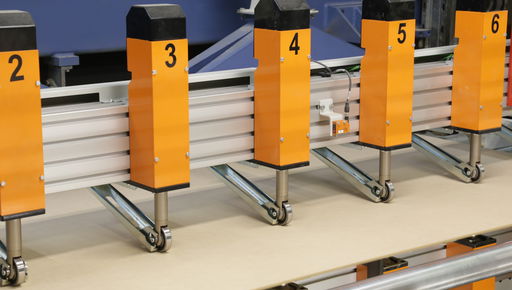
Increasing production speeds place ever higher demands on the performance of inline measuring systems. In order to meet these requirements, continuous improvements and further developments of existing measuring systems are essential. The new version of the GreCon THICKNESSCONTROL RT thickness gauge is an excellent example of this kind of successful improvement. Already established for years in the wood-based materials industry, the contacting thickness measuring system delivers reliable thickness measurement values even at the highest production speeds thanks to new powerful sensor technology. Design changes make THICKNESSCONTROL RT even more robust, maintenance-friendly and energy-efficient.
Measured values - fast and reliable
High production speeds, ever smaller panel gaps - even in today's highly demanding production environment, the new THICKNESSCONTROL RT delivers reliable thickness measurement values as usual. Equipped with quick-switch valves and a high-resolution non-contact measuring sensor, almost the entire plate length is detected even at these high production speeds. The extremely fast automatic calibration also works with very small plate gaps. Permanently reliable measured values are the result.
Reduced maintenance
Maintenance of the new THICKNESSCONTROL RT has been greatly simplified. Design changes have drastically reduced the number of installed parts and hence also the potential sources of error. The upper and lower measuring heads of the new THICKNESSCONTROL RT are identical in construction. The stocking of spare parts is simplified and storage costs are reduced.
The housing of the new top and bottom measuring head is more robust than before thanks to the modified design. This makes the sensor technology even better protected against damage.
Minimal compressed air requirement
The compressed air requirement has been reduced by 80%. Against the background of high energy costs, this minimal compressed air requirement also contributes to energy saving and hence cost reduction.